- Overview
- Company Profile
- Product Details
- Product Parameters
- Packaging & Shipping
- Customer Visiting
- Application
- Factory Equipment
- Qualification
Basic Info.
Product Description
Jiangsu HYT International Trading Co.,Ltd was established in 2015, which is a wholly-owned subsidiary of Wuxi Lusheng Special Steel Co., Ltd., Jiangsu HYT International Trading Co.is responsible for the overseas marketing business of various metal products produced by our group. We specialize in alloy steel, stainless steel, carbon steel, copper, aluminum, high nickel chromium alloy and other materials of pipes, plates, bars, profiles, piping fittings and welding materials. In order to meet our customer's different kinds of demand, we developed other new items too, such as cold drawn section steel, finned tubes, honed tubes, piston rods, forgings and castings, also some customized processing products. We dediceted in providing one-stop service for petroleum, chemical, electric power and automobile manufacturing industries.
Our group is a modern industrial enterprise integrating production, development, sales and service.. We have a complete and effective quality management and quality assurance system, we had passed the ISO 9001:2008 Quality Management System Certification, the National Special Equipment Manufacturing License (Pressure Pipeline Level A2), ISO 14001:2004 Environmental Management System Certification, OHSAS18001:2001 Occupational Health and Safety Management System Certification and Classification Society Certification.
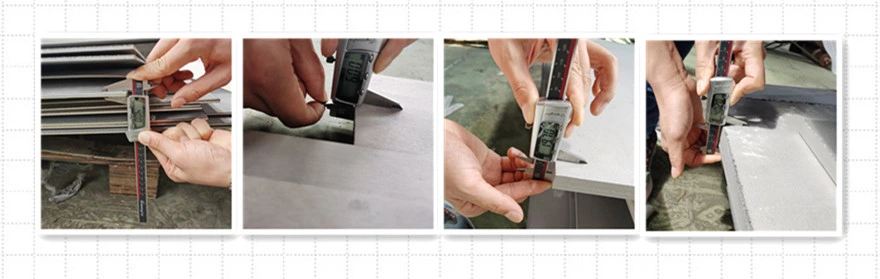
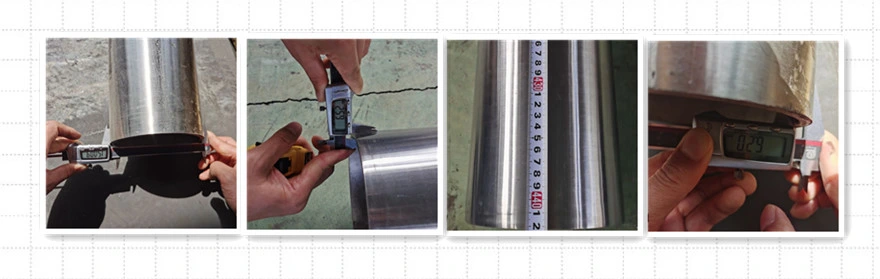
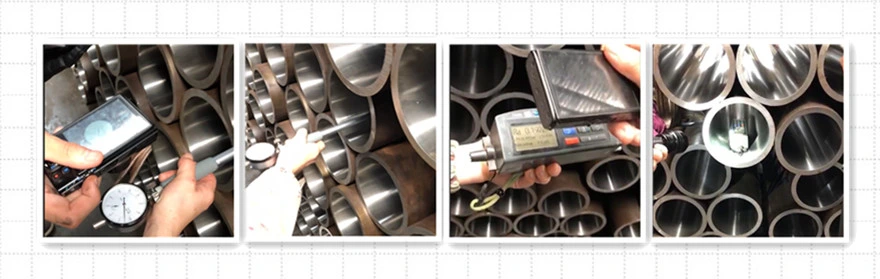
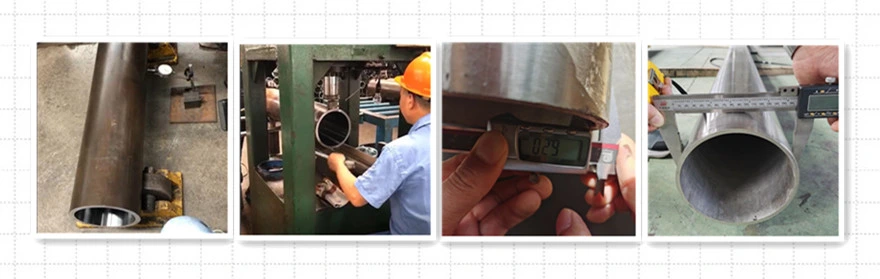
Nicrofer 5923 hMo - Alloy 59
Nicrofer 5923 hMo is a nickel-chromium-molybdenum alloy. Its extremely low silicon and carbon content provides excellent corrosion resistance and very high mechanical strength.
Nicrofer 5923 hMo has the following characteristics:
-In oxidising and reducing states. Excellent corrosion resistance to most corrosive media.
-Excellent resistance to pitting corrosion, crevice corrosion and chloride induced stress corrosion.
-Excellent resistance to inorganic acids. Nitri.c acid, phosphoric acid, sulphuric acid and hydrochloric acid, for example. Especially to a mixture of sulphuric and hydrochloric acids.
-Excellent resistance to a wide range of inorganic acids in mixed solutions.
-Good corrosion resistance in various concentrations of hydrochloric acid solutions up to 40 °C (104 °F).
Good workability and weldability, no susceptibility to post-weld cracking.
-Certified for the manufacture of pressure vessels with wall temperatures from -196 to 450 °C.
-Certified by the American Society of Corrosion Engineers NACE standard (MR-01-75) as meeting the highest standard class VII for use in sour gas environments.
Grade and Standard:
Table 1
Grade and Standard | Material & Grade | Specification | |||||||
Tube/Pipe | Plate | Bar | Strip | Welded Wire | Forgings | ||||
Seamless Steel Tube/ Pipe | Welded Steel Tube/Pipe | ||||||||
German VdTUV | W.Nr.2.4605 NiCr23Mol6Al | 505 | 505 | ||||||
France AFNOR | |||||||||
English BS | |||||||||
America ASTM ASME | UNS N06059 | B622 SB622 | B619/626 SB619/626 | B575 SB575 | B574 SB574 | B575 SB575 | B564 SB564 | ||
ISO |
Chemical Composition (%)
Table 2
Ni | Cr | Fe | C | Mn | Si | Mo | Co | Al | P | S | |
Min | Remain | 22.0 | 15.0 | 0.1 | |||||||
Max | 24.0 | 1.5 | 0.01 0 | 0.5 | 0.10 | 16.5 | 0.3 | 0.4 | 0.015 | 0.005 |
Physical Property
Table:3
Destiny: 8.6 g/cm³
Melting point: 1310-1360 ºC
Temperature | Specific heat capacity | Thermal conductivity | Electrical resistivity | Modulus of elasticity | Coefficient of expansion |
C | J/Kg K | W/m K | u Q cm | KN/mm2 | 0.000001/K |
20 | 414 | 10.4 | 126 | 21C | |
93 | |||||
100 | 425 | 12.1 | 127 | 207 | 11.9 |
200 | 434 | 13.7 | 129 | 20C | 12.2 |
204 | |||||
300 | 443 | 15.4 | 131 | 19E | 12.5 |
316 | |||||
400 | 451 | 17.0 | 133 | 19C | 12.7 |
427 | |||||
500 | 459 | 18.6 | 134 | 18S | 12.9 |
538 | |||||
600 | 464 | 20.4 | 133 | 17E | 13.1 |
Mechanical properties
The following are the properties of cold and hot formed Nicrofer 5923hMo in the corresponding softened condition.
The special properties of other special grades depend on the specific application.
Product | Size mm | Yield Strength Rp0.2 N/mm2 | Yield Strength Rp1.0 N/mm2 | Tensile Strength Rm N/mm2 | Elongation % |
Sheet,Strip/Cold Rolled | 0.5-6.4 | ||||
Plate/Hot Rolled | 5.0-30 | 340 | 380 | 690 | 40 |
Bars, Forgings | ≤100 | ||||
Bars, Forgings | >100 | 320 | 360 | 650 | 40 |
Temperature | Yield Strength Rp0.2 N/mm2 | Yield Strength Rp1.0 N/mm2 | Tensile Strength Rm N/mm2 | Elongation % |
93 | 50% | |||
100 | ≥290 | ≥330 | 650(620) | |
200 | ≥250 | ≥290 | 615(585) | |
204 | ||||
300 | ≥220 | ≥260 | 580(550) | |
316 | ||||
400 | ≥190 | ≥230 | 545(515) | |
427 | ||||
450 | ≥175 | ≥215 | 525(495) |
ISO V-notch impact strength
Room temperature average: ≥ 225 J/cm2
At -196°C ≥ 200 J/cm2
Metallographic structure
Nicrofer 5923 hMo is a face-centred cubic lattice structure
Corrosion resistance
The nickel-chromium-molybdenum alloy Nicrofer 5923 hMo, with its very low carbon and silicon content, has no tendency to precipitate impurity phases during hot working and welding and is therefore suitable for use in various chemical process industries containing oxidising and reducing media. The high content of molybdenum and lead makes the alloy resistant to chloride ions.
Nicrofer 5923 hMo outperforms other Ni-Cr-Mo stainless steels in most standard corrosion tests in oxidising environments. hMo corrodes more than three times less than conventional Ni-Cr-Mo stainless steels in some reducing environments (e.g. boiling 10% sulphuric acid) and is also suitable for use in chemical process industries in reducing environments. The corrosion rate is three times lower than that of conventional Ni-Cr-Mo stainless steels in some reducing environments (e.g. boiling sulphuric acid). Figure 3 shows the excellent corrosion resistance of Nicrofer 5923 hMo in hydrochloric acid.
Alloys only have the best corrosion resistance when they are in a suitable metallurgical state and have a pure crystal structure.
Temperature. °F
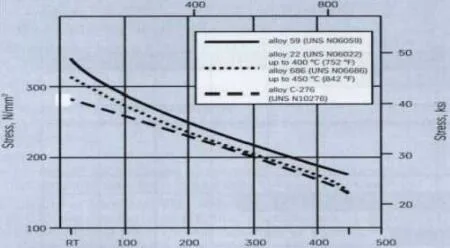
Temperature. "C
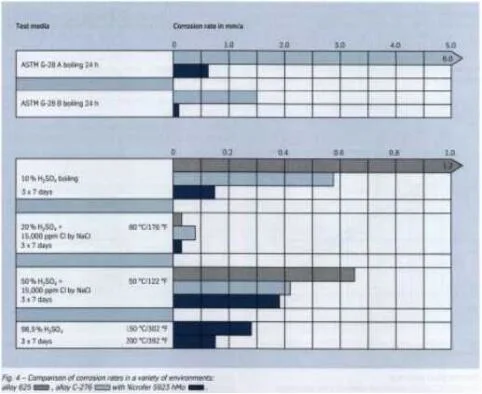
Fig. 1: Comparison of Rp0.2 yield strength values of alloy 59 with other nickel-based alloys
Fig. 4: Corrosion rates in different corrosive environments
Range of applications
Nicrofer5923hMo has a wide range of applications in the chemical, petrochemical, energy manufacturing and pollution control sectors. Typical applications are as follows.
-especially when using acid chloride catalysts
-Boilers and bleaching equipment in the pulp and paper industry
- Scrubbers, reheaters, throttle valves, wet vapour fans and agitators in FGD and IG systems
-Equipment and components for operation in sour gas environments
-reactors for acetic acid and vinegar liver products
-Sulphuric acid condensers
Machining and heat treatment
Nicrofer 923 hMo alloy has excellent cold and hot working and machining properties.
Heating
1. The workpiece should always be clean and free from contamination before and during the heat treatment.
2. Do not contact sulphur, phosphorus, lead and other low melting point metals during the heat treatment as this may impair the properties of Nicrofer 5923 hMo alloy. Care should be taken to remove contaminants such as marking paint, temperature indicating paint, coloured crayons, lubricants, fuel etc.
3. The lower the sulphur content of the fuel, the better. The sulphur content of natural gas should be less than 0.1% and the phosphorus content of heavy oil should be less than 0.5% o
4. Taking into account the need for temperature control and cleanliness. The heat treatment should preferably be carried out in a vacuum or gas-protected furnace.
It can also be heated in a chamber furnace or a gas furnace. However, the furnace gas must be clean and neutral to slightly oxidising, avoiding fluctuations between oxidising and reducing properties. The heating flame must not be directed towards the workpiece.
Hot Processing
1. Nicrofer 5923 hMo can be hot worked in the temperature range of 1180°C to 950°C with water cooling or rapid air cooling.
2. To ensure optimum corrosion resistance, heat treatment should be carried out after hot working. The workpiece should be added directly to the heated heat treatment furnace.
Cold Processing
1. The work hardening rate of Nicrofer 5923 hMo is greater than that of austenitic stainless steels and therefore requires selection of the processing equipment. The workpiece should be in annealed condition. The cold rolling process should be intermediate annealed.
2. If the cold rolled deformation is greater than 15%, the workpiece should be solid solution treated.
Heat treatment
1. The solid solution treatment temperature range for Nicrofer 5923 hMo is 1100°C - 1180°C.
2. For materials less than 1.5 mm thick the recommended cooling method is water quenching or rapid air cooling to ensure the best corrosion resistance.
3. In all heat treatment processes. Workpieces should be added directly to the heated heat treatment furnace and must be kept clean.
Oxide removal
1. Nicrofer 5923 hMo has a stronger adhesion to surface oxides and slag around the weld seam than stainless steel. It is recommended to use fine grain abrasive belts or fine grain abrasive wheels for grinding.
2. The oxide film must be broken up by careful sanding or salt bath pre-treatment before pickling with a HNOj/HF acid mixture for the appropriate time and temperature.
Machining
Nicrofer 5923 hMo should be machined after heat treatment. Due to the work-hardening of the material, it is advisable to use lower cutting speeds and heavy feeds than for low-alloyed standard austenitic stainless steels. The material should only be turned below the cold-hardened surface layer.
Austenitic stainless steels are machined at low cutting speeds and with heavy feeds. It is only possible to turn beneath the cold-hardened surface layer.
Welding advice
When welding nickel-based materials. The following procedures should be followed.
1. Workplace
The workplace should be separate or sufficiently distant from the area where carbon steel is processed. Keep it as clean as possible. Partitions should be provided and communication between the two areas should be avoided.
2. Work clothing and aids
Clean, fine grain leather gloves and clean work clothes should be worn.
3. Tools and machines and equipment
There should be special tools for nickel-based alloys and nickel-lead steel. Steel wire brushes should be made of stainless steel. Machines and equipment such as shears, punches, mills etc. should be covered with felt, cardboard or plastic paper to prevent iron and carbon metal from falling on the surface of the machine and sticking to the material being processed, leading to corrosion.
Cleaning
The material to be welded should be in the solid solution state, with oxides, oils and marks removed and the base metal and filler alloys (e.g. electrodes) in the weld area cleaned with C-profile. Note that trichloroethylene TRI, perchloroethylene PER and tetrachloroethylene TETRA should not be used.
Edge preparation
Preferably machined. e.g. turning, milling, planing. Plasma cutting is also possible, but in the latter case the cut edges (weld surface) must be ground clean and flat. Fine grinding without heat is permitted.
Bevel angle
Compared to carbon steel. The physical properties of nickel-based alloys and special stainless steels are mainly characterised by low thermal conductivity and high expansion coefficients, which should be taken into account when preparing the weld bevel, including widening the bottom gap (l_3mm), and due to the viscosity of the molten metal, a larger bevel angle (60° to 70°) should be used when butt welding to offset the shrinkage of the material.
Starting the arc
The arc should be started in the welding area of the workpiece, i.e. on the welding surface. This is to prevent the arc starting point from causing corrosion.
Welding process
Nicrofer 5923 hMo can be welded with homogeneous materials or other metals. It is suitable for welding with any conventional welding process, such as inert gas shielded welding with aluminium electrodes, iso-arc welding, manual sub-arc welding, metal electrode inert gas shielded welding, molten electrode inert gas shielded welding. Preference is given to pulsed sub-arc welding technology. For manual arc welding, a mixture of Ar+He+H2+CO2 is recommended.
Filler metal
For gas shielded welding. It is recommended to use a welding rod with the same chemical composition as the base material. The filler metals usually used are.
Supply specifications
Nicrofer 5923 hMo alloy is available as a rolled product in the following standard sizes.
Plates and sheets (please refer to strip for specifications for delivery in fixed lengths)
Delivery condition: hot-rolled or cold-rolled in solution-treated condition, pickled
Thickness mm | Cold Rolled/Hot Rolled | Width mm | Length mm |
1.30-<1.50 | Cold Rolled | 2000 | 6000 |
1.50-<6.00 | Cold Rolled | 2400 | 8000 |
6.00-<10.00 | Cold Rolled | 2400 | 8000 |
6.00-<10.00 | Hot Rolled | 2400 | 8000 |
10.00-<25.00 | Hot Rolled | 2400 | 5000" |
>=25.00' | Hot Rolled |
Depends on the weight of the sheet
Round plates and rings
Delivery condition: hot rolled or forged, solid solution treated, pickled or machined
Products | Weight Kg | Thickness mm | Outer Diameter *mm | Inner Diameter * mm |
Round Plate | ≤4000 | ≤200 | ≤2000 | |
Round Ring | ≤3000 | ≤200 | ≤2500 | According to the request |
Wires or filaments
Delivery condition: bright drawn. Bright annealed state.
Specification: ψ 0.01-12.0mm, in coils, barrels, spools or reels.
Bars
Delivery condition: forged, rolled, cold drawn, solid solution treated, pickled, peeled or polished.
Forgings.mm | Rolled Products *mm | Cold Drawn• mm | |
Round Bars(Diameter) | ≤300 | 15-75 | 12-65 |
Bars(Square Section,a) | 40-300 | 15-100 | 12-65 |
Bars(Rectangular Sectionaxb) | (40-80) x (200-600) | (5-20)x(120-600) | (10-20) x (30-80) |
Bars(Hex Section.s) | 40-80 | 13-50 | 12-60 |
Forgings
In addition to round plates, rings, rods and bars, irregularly shaped forgings are also available on request.
Strip
Delivery condition: cold rolled, solution treated. Pickled or bright annealed
Thickness mm | Width mm | Strips Coil Diameter | |||
0.04-<0.10 | 4-200 | 300 | 400 | ||
>0.10-<0.20 | 4-350 | 300 | 400 | 500 | |
>0.20-<0.25 | 4-750 | 400 | 500 | 600 | |
>0.25-<0.60 | 5-750 | 400 | 500 | 600 | |
>0.60-<1.0 | 8-750 | 400 | 500 | 600 | |
>1.0-<2.0 | 15-750 | 400 | 500 | 600 | |
>2.0-<3.0 | 25-750 | 400 | 500 | 600 | |
*Fixed lengths available in sizes 500-3000mm (20 120in) |
Welding filler materials
All standard sizes of rod, wire, strip and flux cored electrodes are available
Seamless Tubes
Seamless tubes are supplied by Thysse.nKrup.p VDM and produced by DMV Stainless.
Welded tubes
Welded tubes are supplied semi-finished by Thysse.nKrup.p VDM and processed by certified manufacturers.
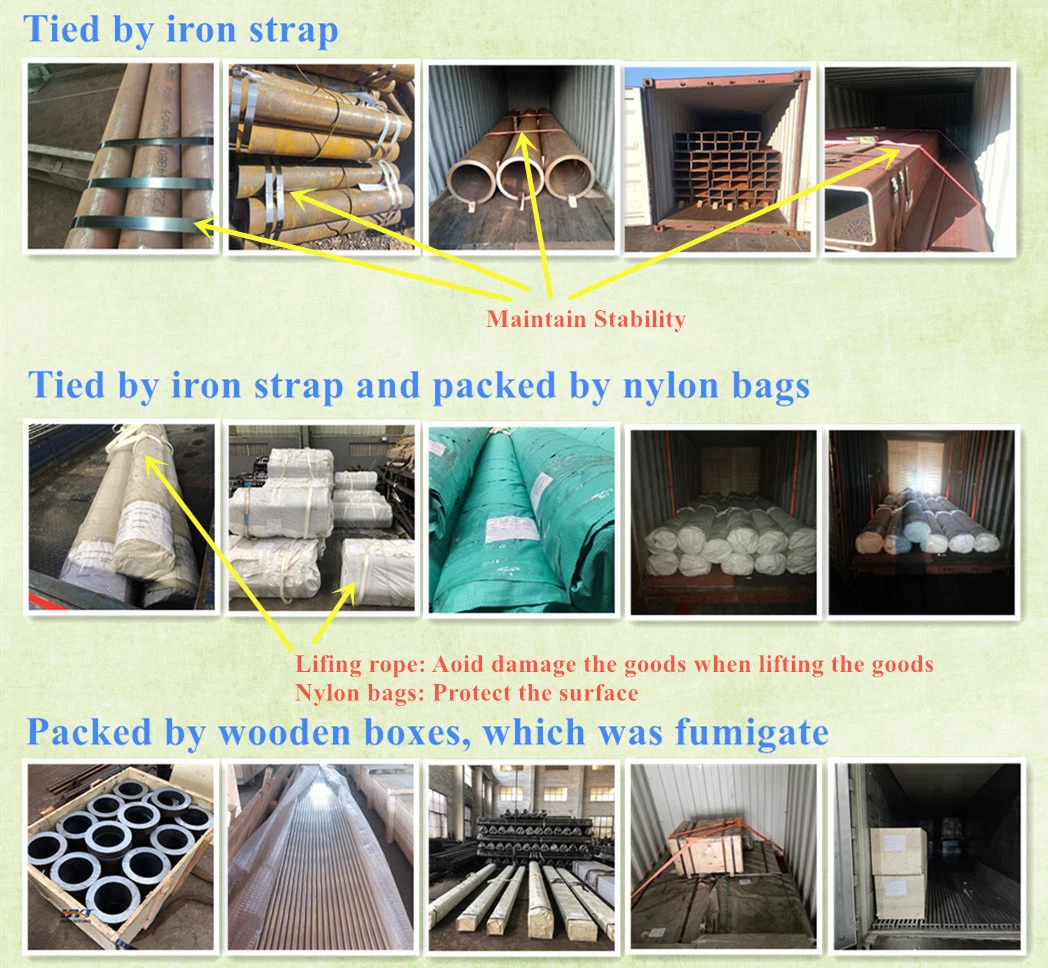
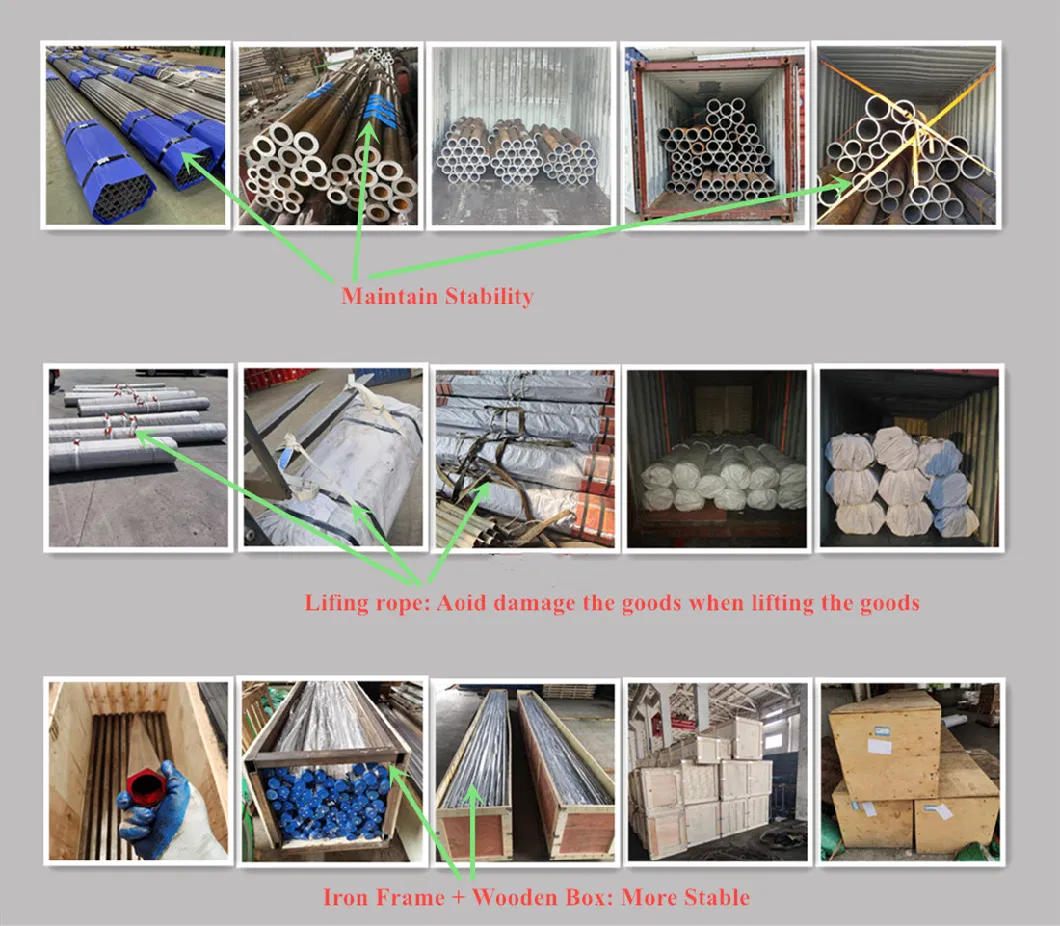
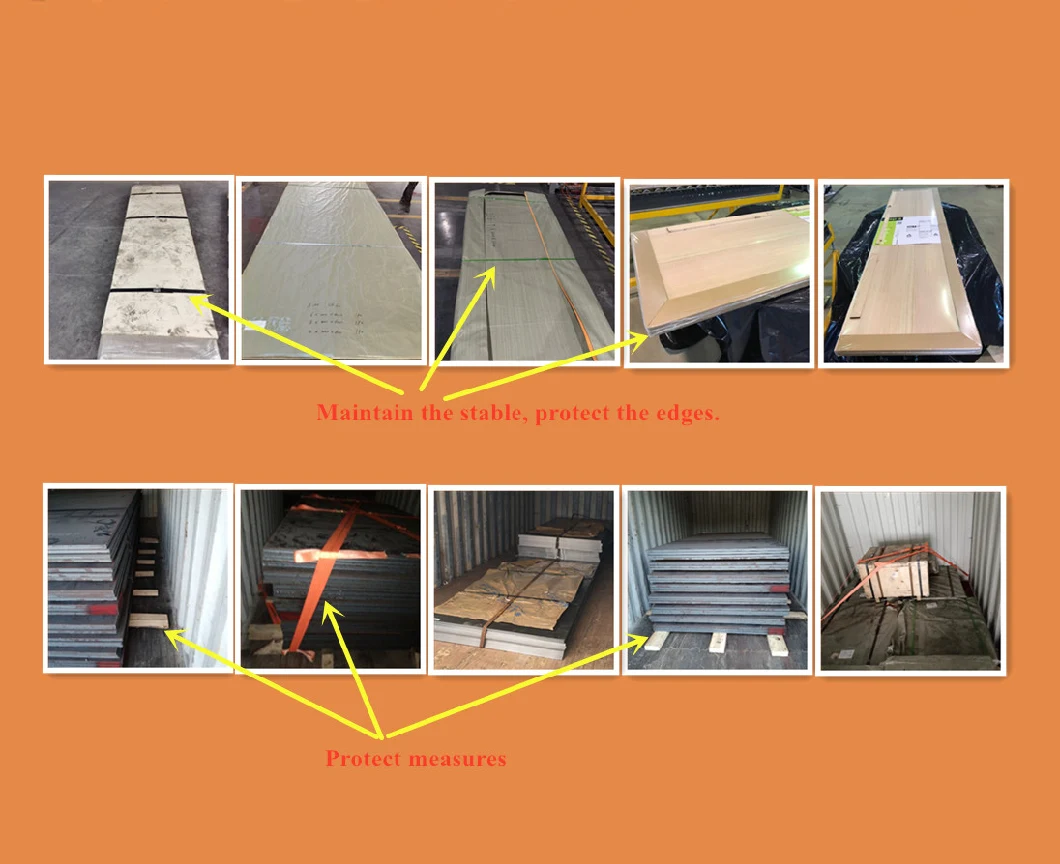
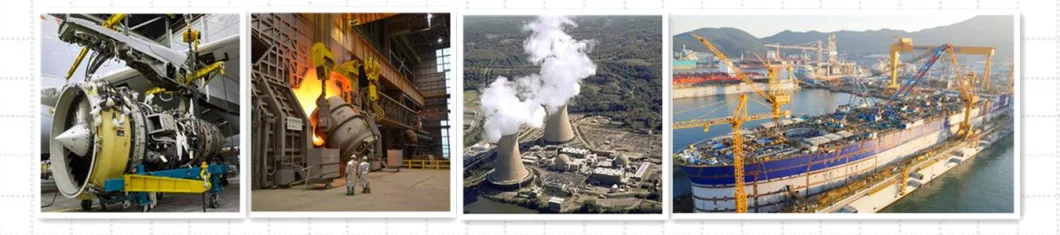
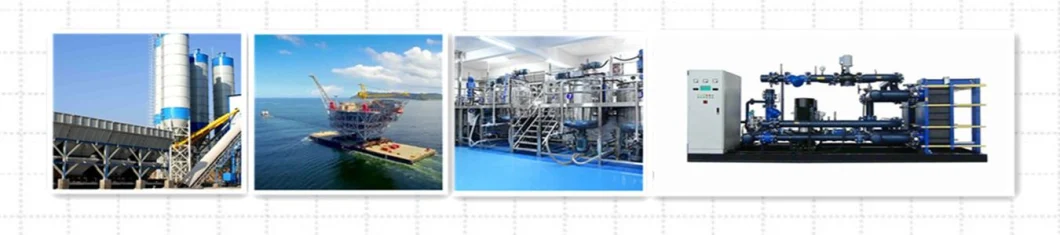
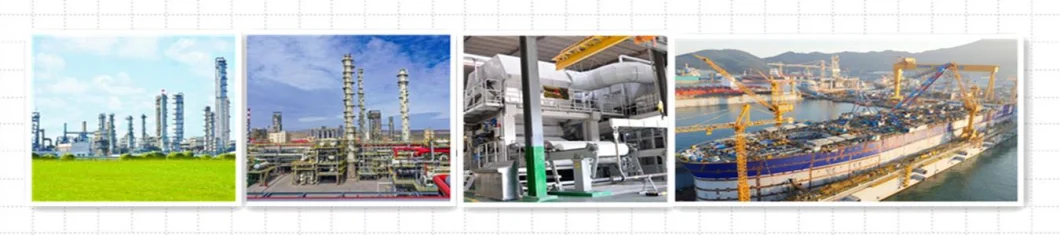
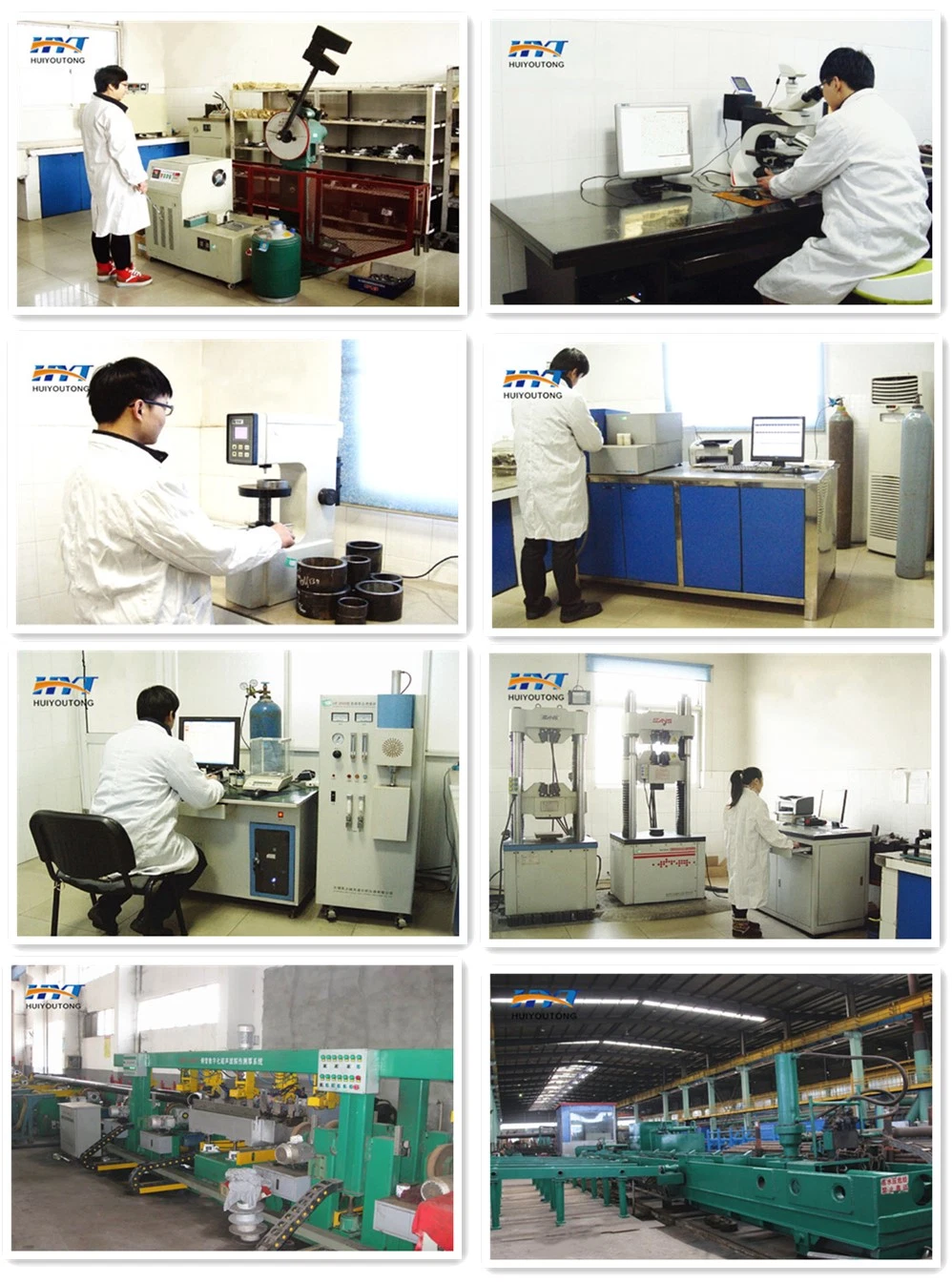
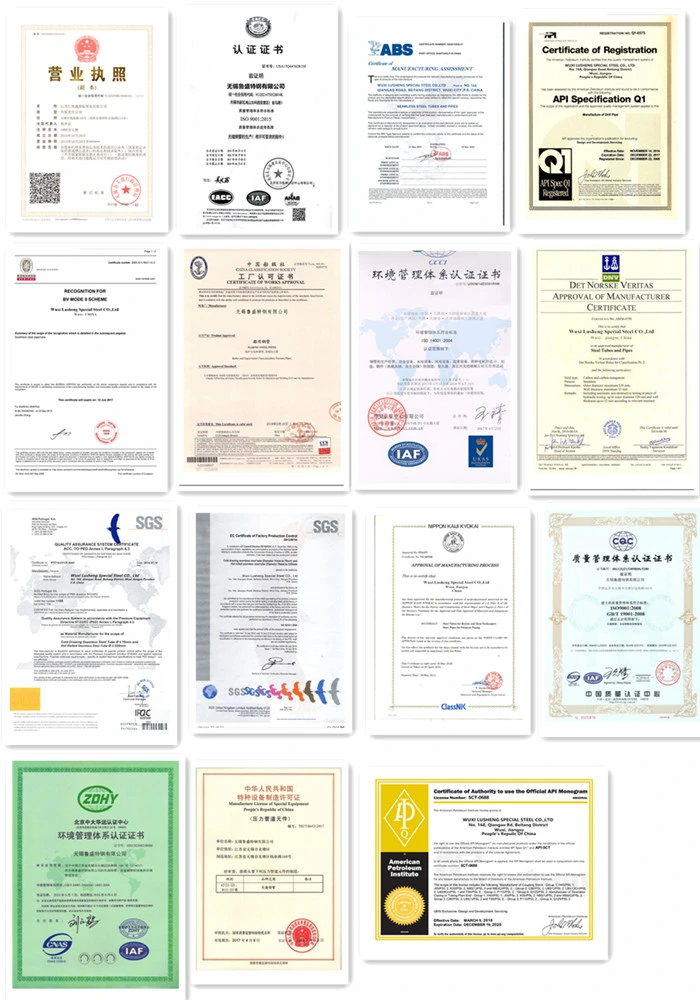