Basic Info.
Model NO.
SF-160KW
The Range of Operating Voltage
340-430V AC
Output Power
200kw
Input Current
300A
Fluctuating Frequency
20-50kHz
Timing (Heat Time,Retain Time,Cool Time)
1-99s
The Flow Rate of Cooling Water
5ton/H
Water Temperature Protection Point
40centidegree
Principle
Induction Heating
Structure Material
Metal Material
Heat Transfer Surface
Tubular Heat Exchanger
Transport Package
Exported Wooden Box
Specification
CE, ISO EU
Trademark
ORD
Origin
Foshan
HS Code
8514400090
Production Capacity
1000000/Year
Product Description
CE IGBT Super High Frequency Induction Heating Machine of Heat Treatment of Engine Block Parts (crankshafts, camshafts, valves, starting rings)
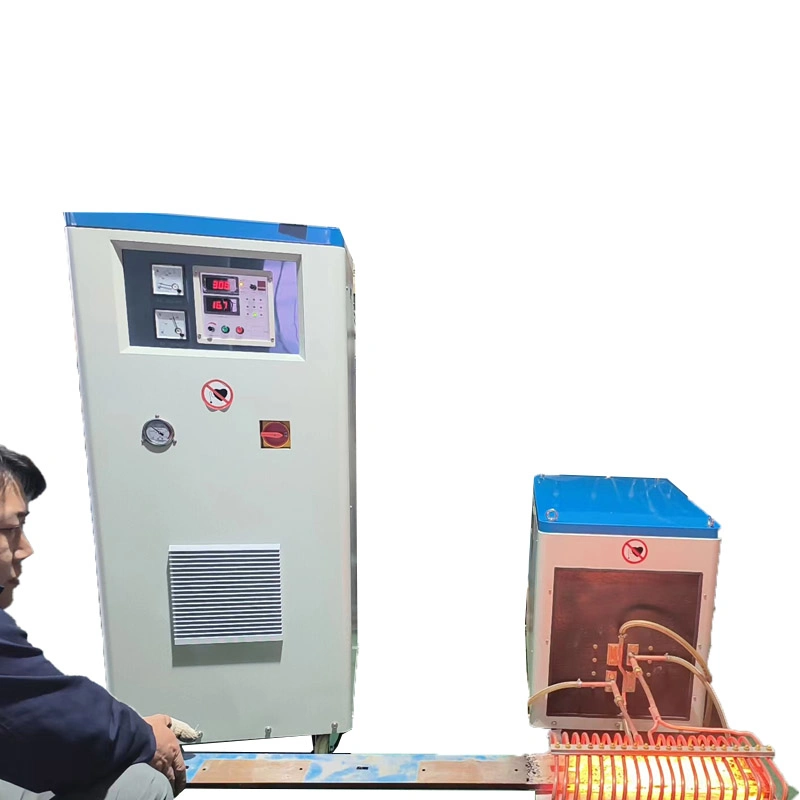
INDUCTION HEATING MACHINE :
Induction heating is a process which is used to bond, harden or soften metals or other conductive materials. For modern manufacturing processes, induction heating offers an attractive combination of speed, consistency, control and energy efficiency.
The basic principles of induction heating have been understood and applied to manufacturing since the 1920s. During World War II, the technology developed rapidly to meet urgent wartime requirements for a fast, reliable process to harden metal engine parts.
More recently, the focus on lean manufacturing techniques and emphasis on improved quality control have led to a rediscovery of induction technology, along with the development of precisely controlled, all solid state induction power supplies.
How induction heating works?
When an alternating electrical current is applied to the primary of a transformer, an alternating magnetic field is created. According to Faraday's Law, if the secondary of the transformer is located within the magnetic field, an electric current will be induced.
In a basic induction heating setup, a power supply sends an AC current through an inductor (often a copper coil), and the part to be heated (the workpiece) is placed inside the inductor. The inductor serves as the transformer primary and the part to be heated becomes a short circuit secondary. When a metal part is placed within the inductor and enters the magnetic field, circulating eddy currents are induced within the part.
Induction heating is a process which is used to bond, harden or soften metals or other conductive materials. For modern manufacturing processes, induction heating offers an attractive combination of speed, consistency, control and energy efficiency.
The basic principles of induction heating have been understood and applied to manufacturing since the 1920s. During World War II, the technology developed rapidly to meet urgent wartime requirements for a fast, reliable process to harden metal engine parts.
More recently, the focus on lean manufacturing techniques and emphasis on improved quality control have led to a rediscovery of induction technology, along with the development of precisely controlled, all solid state induction power supplies.
How induction heating works?
When an alternating electrical current is applied to the primary of a transformer, an alternating magnetic field is created. According to Faraday's Law, if the secondary of the transformer is located within the magnetic field, an electric current will be induced.
In a basic induction heating setup, a power supply sends an AC current through an inductor (often a copper coil), and the part to be heated (the workpiece) is placed inside the inductor. The inductor serves as the transformer primary and the part to be heated becomes a short circuit secondary. When a metal part is placed within the inductor and enters the magnetic field, circulating eddy currents are induced within the part.
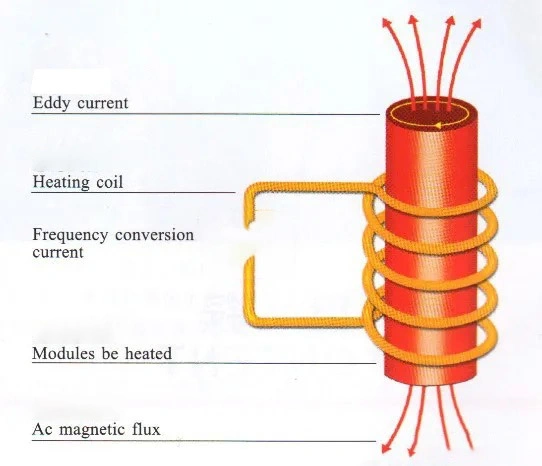
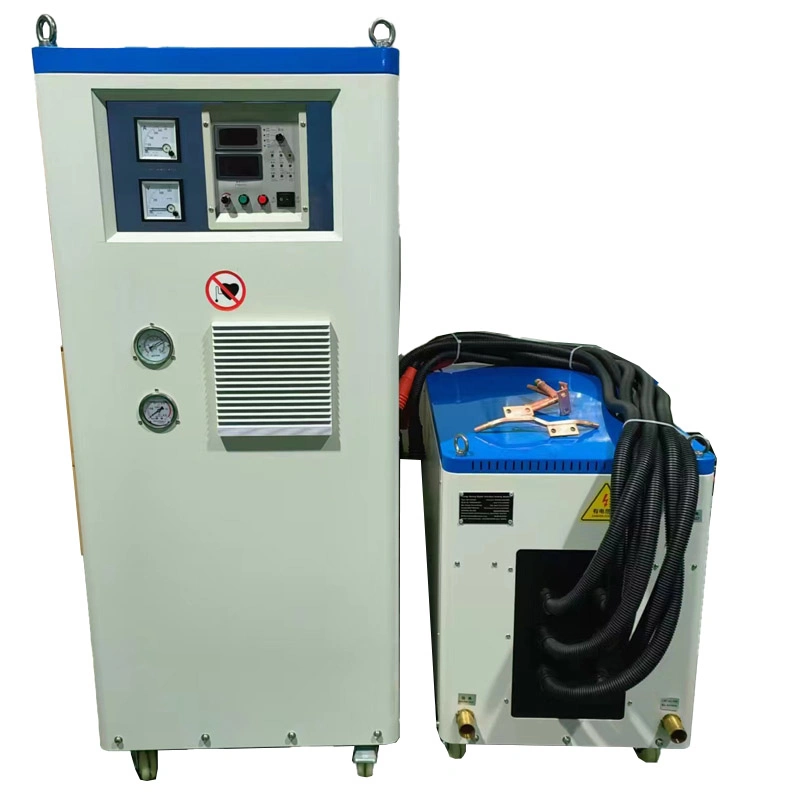
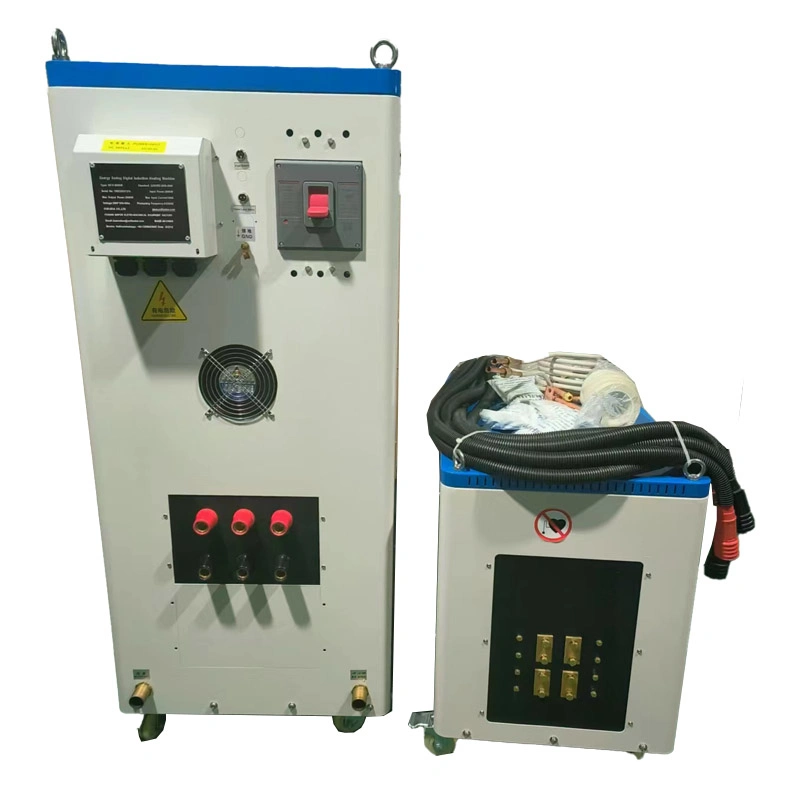
Main characteristics:
1 Infineon IGBT module and Inverting technologies of third generation been used; Higher reliability and lower maintenance cost.
2 100% Duty cycle, continuous working is allowed at maximum power output.
3 Constant current or constant power status can be selected accordingly to achieve higher heating efficiency;
4 Display of heating power and heating current and oscillating frequency;
5 Simple to install, Installation can be done by unprofessional person very easily;
6 Light weight
7 Advantages of the model with timer: the power and the operating time of the heating period and the retain period can be preset respectively, to realize a simple heating curve, this model is suggested to use for batch production to improve the repeatability;
8 The separated models are designed to fit the dirty surrounding of some cases.
9 Main part control two transformers, install AC contactor can control any one transformer to work automatically.
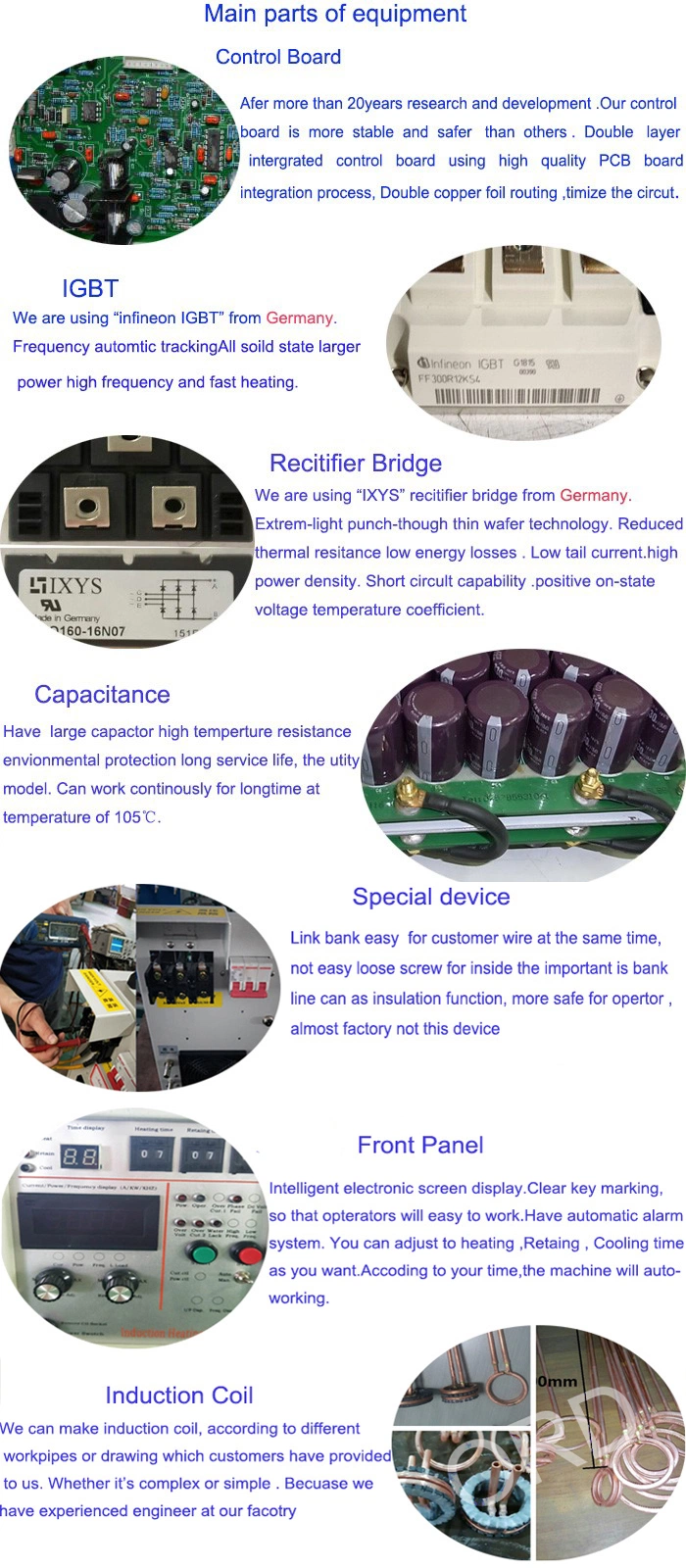
APPLICATIONS :
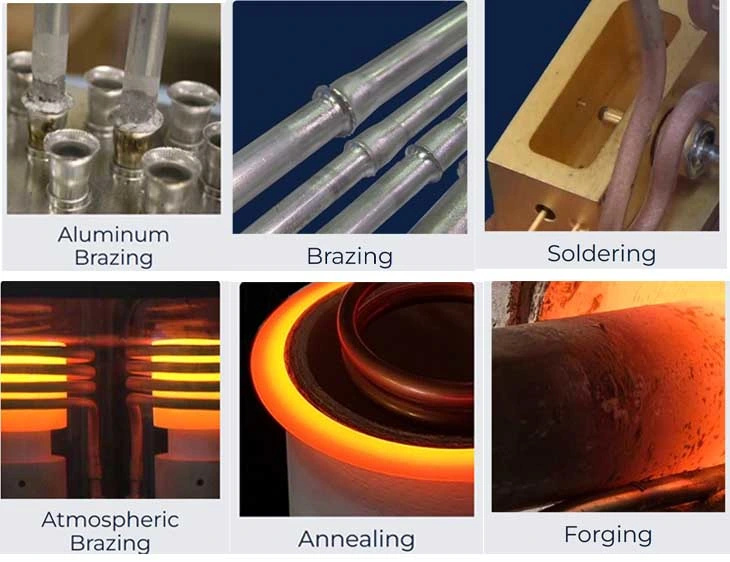
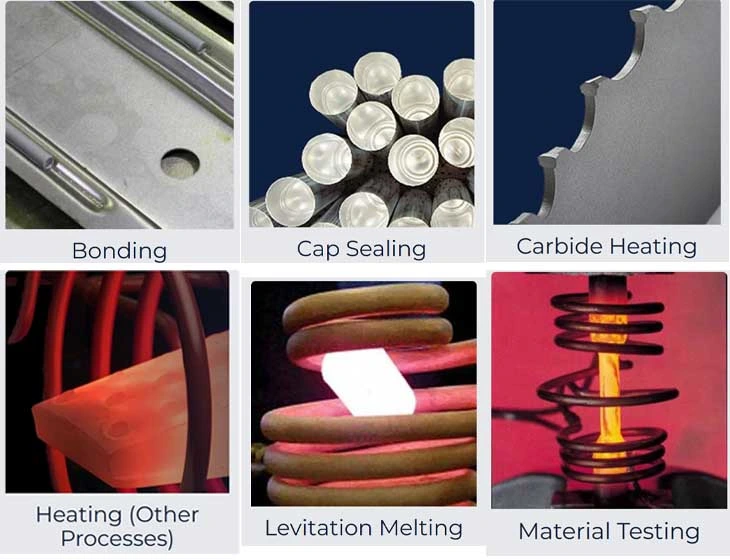
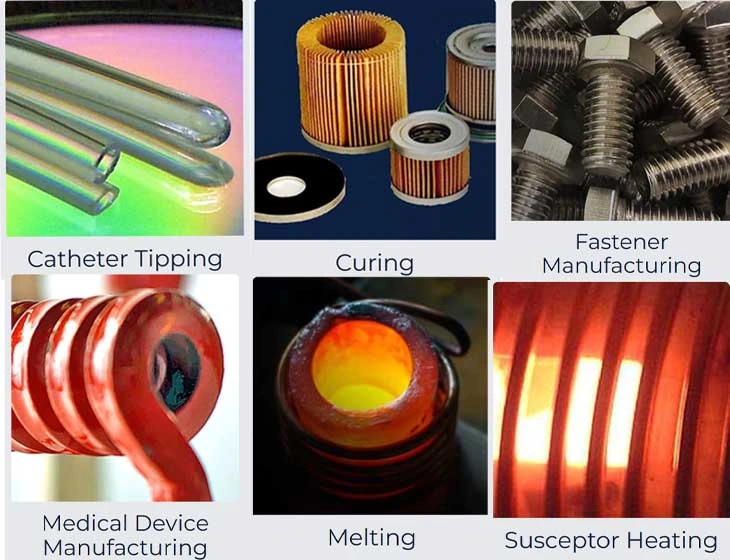
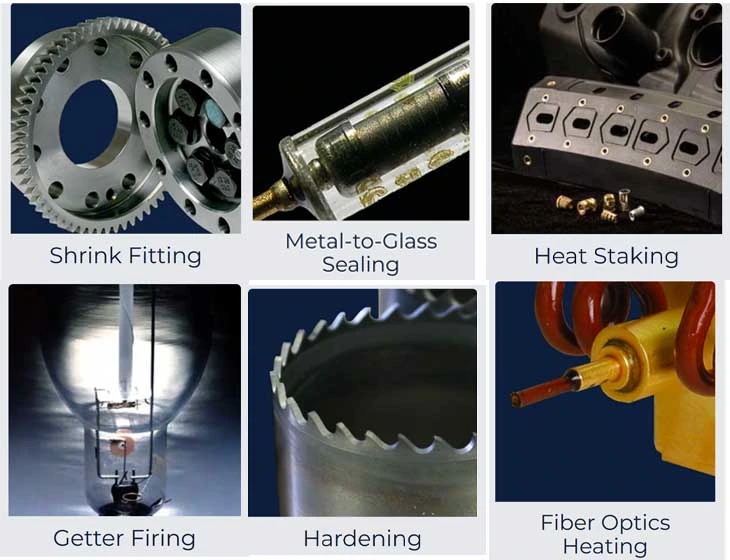
Type | SF-160KW |
Work power | 3×380V(415V,440V,480V)50-60HZ |
The range of operating voltage | 340V-430V(370-480)V AC |
Output power | 160 KW |
Input current | 240A |
Fluctuating frequency | 20-50KHZ |
Timing (Heat time, Retain time , Cool time) | 1-99S |
The flow rate of cooling water | 5TON/H |
Water temperature protection point | 40 C |
Duty cycle | 100% (40degree room temperature) |
Weight | Main parts: KG Transformer parts : KG |
Size | Main Parts: 880*600*1350MM Transfromer Parts: 780*450*700MM |
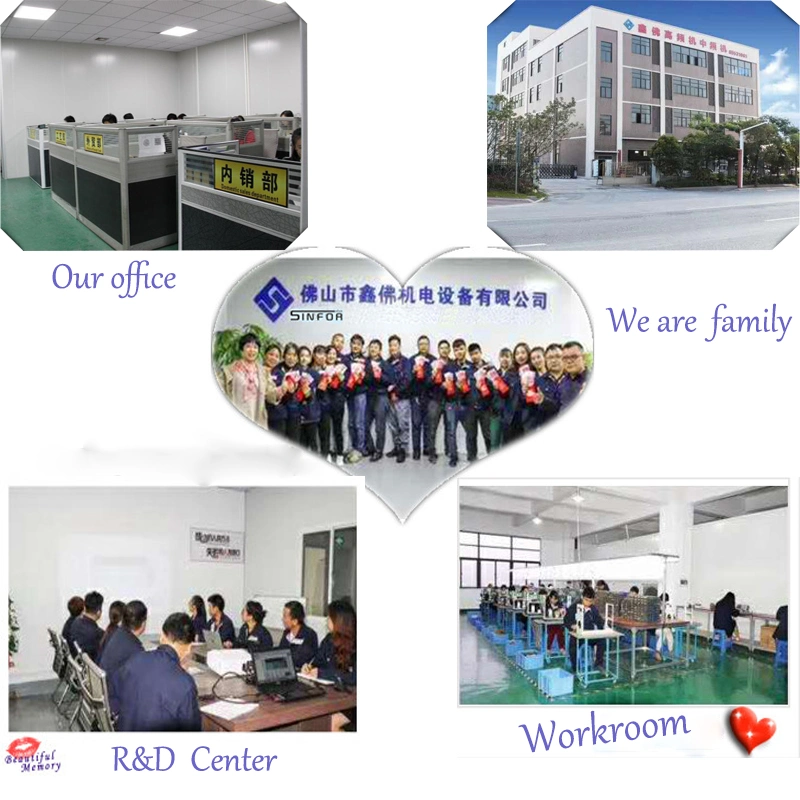
Pre-sale service:
1. recommend the most suitable machine for customers, according to their requirements.
2. Inquiry and consulting support.
3. Sample testing support.
4. View our Factory.
In-sale service:
1. Strictly manufacture the machine, according to relevant technical standards.
2. Take run test, according to relevant equipment test run regulations.
3. Strictly check up the machine, before delivery
4. Delivery on time.
After-sale service:
1. Warranty time: Within 18 months from the date of delivering, 12months from date of receiving.
2. Within warranty all parts are free for customer, any fault caused by non-artificial reason, any quality problems such as design, manufacture, or procedure occurs, We shall provide replacement parts after detecting the faults.
3. If any big quality problems occurs out of the guarantee period, we will send maintenance
technician to provide visiting service after checking with the customer and charge for a favorable price.
5. We will provide a lifetime cost price to the buyer with the materials and spare parts used in system operation, equipment maintenance.
6. The above mentioned are only basic aftersale service requirements,we will make more promises related to quality assurance and operation guarantee.
