- Overview
- Product Description
- Product Parameters
- Detailed Photos
Basic Info.
Model NO.
painting line
Application
Hardware Spraying Equipment, Wood Spraying Equipment, Plastic Spraying Equipment, Porcelain Spraying Equipment
Coating
Paint
Certification
CE, ISO
Method Type
Automatic
Condition
New
Stages
Single or Multiple Stages
Important Features1
The Ability to Handle Tight Curves
Important Features2
The Ability to Withstand Harsh and Corrosive
Customized Type1
Enclosed Track Conveyor
Customized Type2
Power and Free Conveyor
Customized Type3
Heavy Duty Conveyor
Customized Type4
I-Beam Conveyor
Transport Package
Polyfoam and Metal Frame
Specification
CE, EU standard
Trademark
INFITECH
Origin
Guangzhou, Guangdong, China
HS Code
8419899090
Production Capacity
200sets/Year
Packaging & Delivery
Package Size
1600.00cm * 230.00cm * 230.00cm
Package Gross Weight
5600.000kg
Product Description
Conveyors for Cleaning and Pre-treatment
INFITECH provides cleaning and pre-treatment conveyors to assist in the process flow of the entire painting line.
In paint factories, every common painting and finishing operation from wet spraying and electronic coating to powder coating and electroplating involves one or more pre-treatment processes, which need to be completed before the final painting or topcoat coating process. Surface pre-treatment typically involves passing the finished product through a series of chemical baths and rinsing, aiming to clean the surface and remove grease, soil, oxides, and other materials. According to the characteristics of different workpieces, they will undergo other processes including pickling, phosphating, sandblasting, and drying, as well as pre-treatment and surface treatment.
INFITECH has extensive experience in supporting elevated conveyors, which have been proven to be excellent solutions for handling products in all stages of precision machining pre-treatment and surface treatment. All of our cleaning and pre-treatment conveyors are designed and manufactured to withstand the harsh chemicals involved in these processes.
A typical three-stage system consists of the following | A typical three-stage system consists of the following |
|
|
2.PROJECT CASE
Conveyors for Cleaning and Pre-treatment

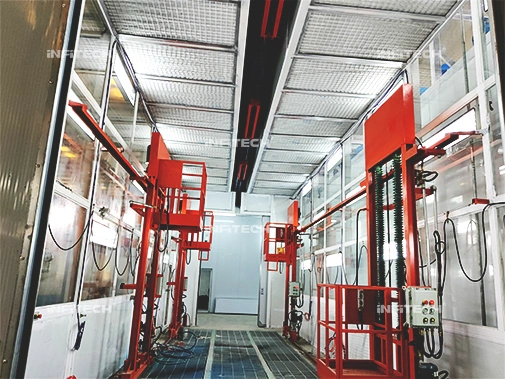
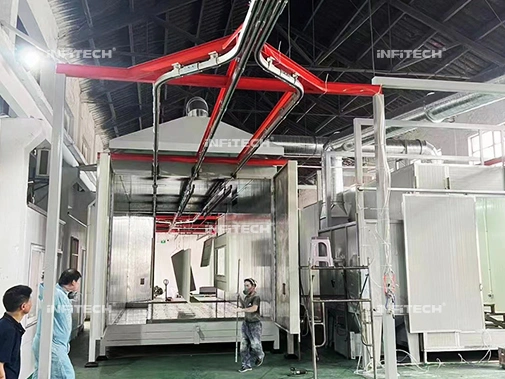
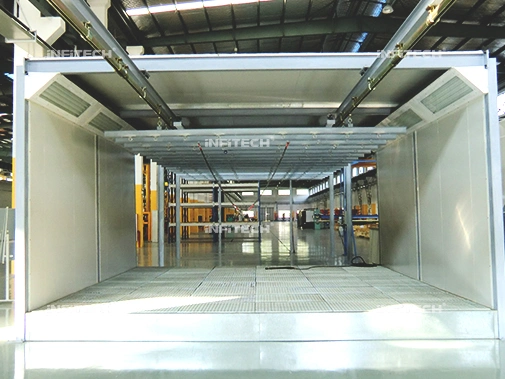
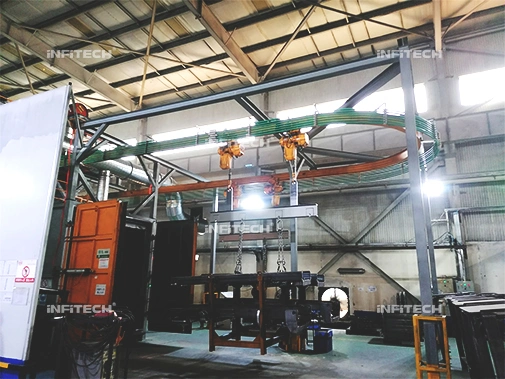
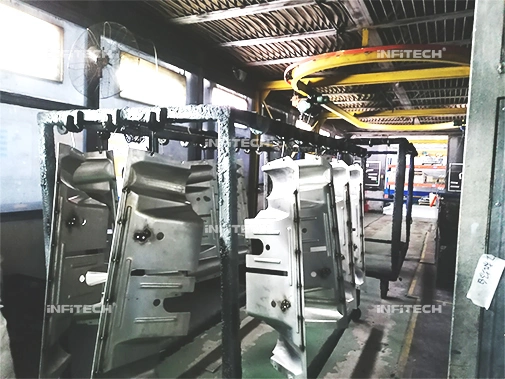