Basic Info.
Customized
Non-Customized
Condition
New
After-sales Service
a Lifetime
Screw Diamter
20mm
Screw Length
325mm
Screw Types
Many
Die Heads
Many
Barrel Structure
Pull and Turn
Heating
Electrical Heating/4 Zones
Cooling
Air Compressed
Transport Package
Plywood
Trademark
Hapro
Origin
China
HS Code
9024800000
Production Capacity
100/Year
Product Description
Laboratory Conical Twin-screw Extruder can be integrated by main unit and conical twin-screw extrusion unit. That can be used to simulate real production process in the laboratory.Because of its special structure, the residual material can be cleaned quickly. In the measuring extrusion unit, the sample material begin plastify under practice-oriented conditions and extruded through the die head.Matched well with different die heads ,it's used for extruding the Belt, Tube, PCPO and granulation .
Conical Twin-screw platform is consist of the Drive device, Feeding device, Barrel ,Twin-screw and Dies parts, etc. The Twin-screw is the heart of the extruder, divided into the charging section (solid conveying zone), compression section(melting zone) and the homogenization section (the melt conveying zone) three parts. Put the material into the hopper ,under the action of a rotating screw, material was pushed on to the direction of the nose. Material endures strong shear, mixing and calendaring in the barrel, In this process, Meanwhile, the physical states of material the evolve from glass state to the high elastic state ,eventually become sticky flow pattern .
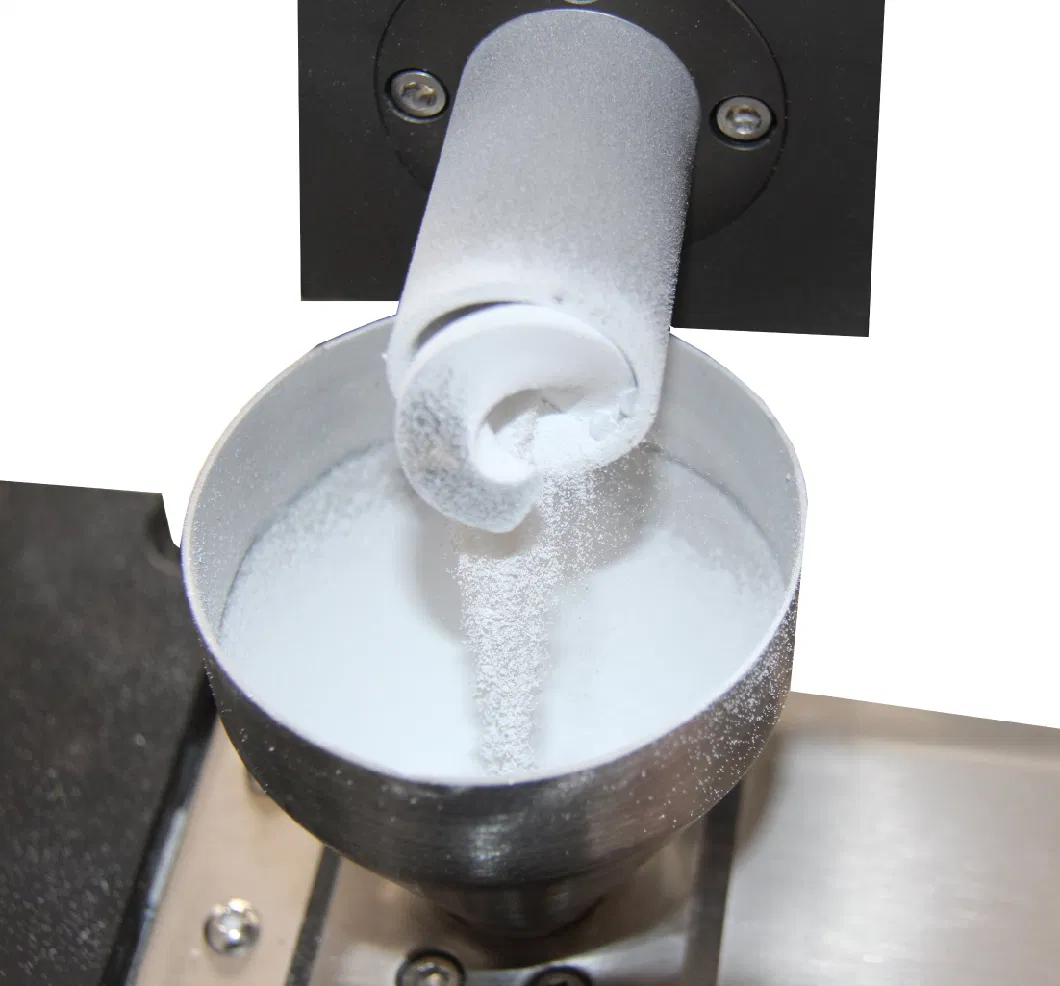
Dies
The Hapro die heads can easily be connected to the different extruders The die heads can be interchanged quickly and easily. They are heated electrically and have a separate control circuit. The die heads can be disassembled for cleaning. Various die heads are available for specific measuring tasks. Conical Twin-screw platform is consist of the Drive device, Feeding device, Barrel ,Twin-screw and Dies parts, etc. The Twin-screw is the heart of the extruder, divided into the charging section (solid conveying zone), compression section(melting zone) and the homogenization section (the melt conveying zone) three parts. Put the material into the hopper ,under the action of a rotating screw, material was pushed on to the direction of the nose. Material endures strong shear, mixing and calendaring in the barrel, In this process, Meanwhile, the physical states of material the evolve from glass state to the high elastic state ,eventually become sticky flow pattern .
- Equipment composition
- Drive device
Feeding device
Conical Twin-screw platform adopts screw metering feeding device. According to the properties of material production and processing technology conditions, adjust the volume of feed speed and extrusion in order to achieve the balance.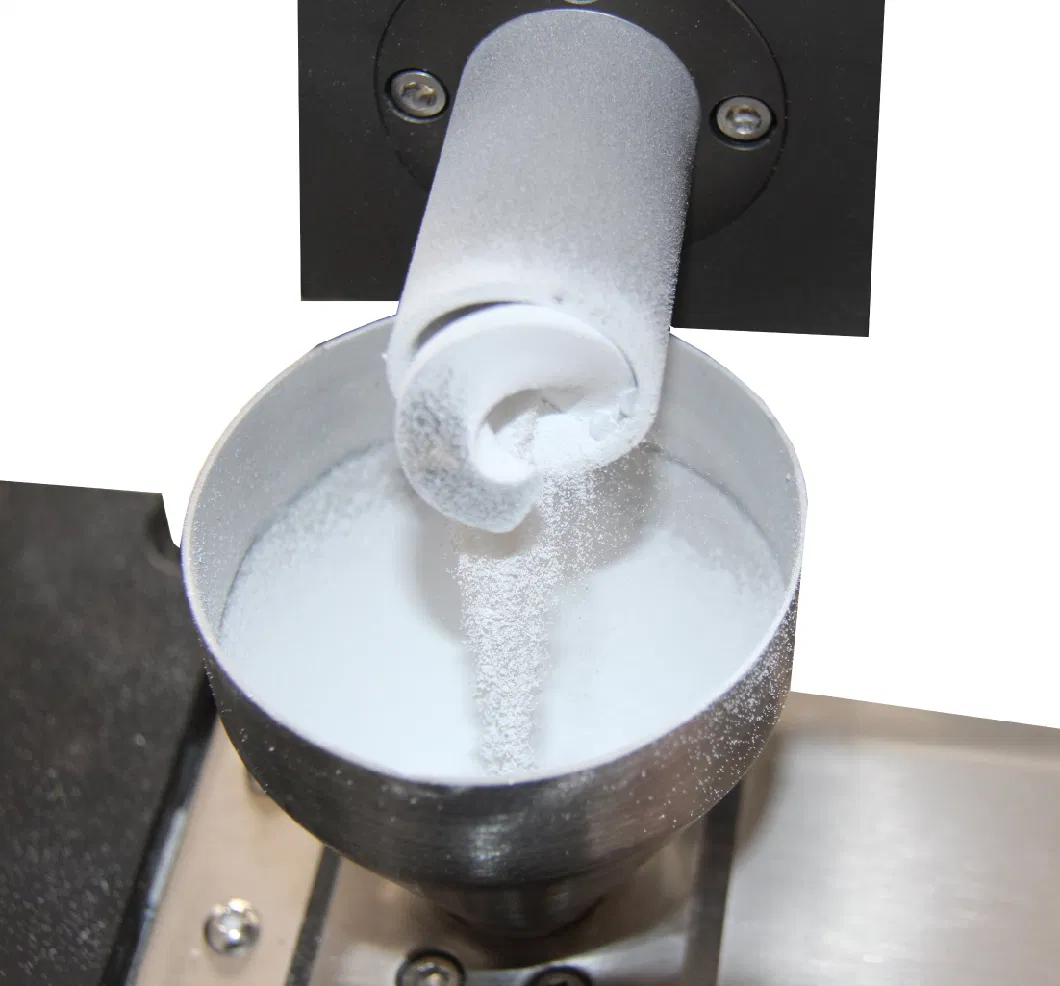
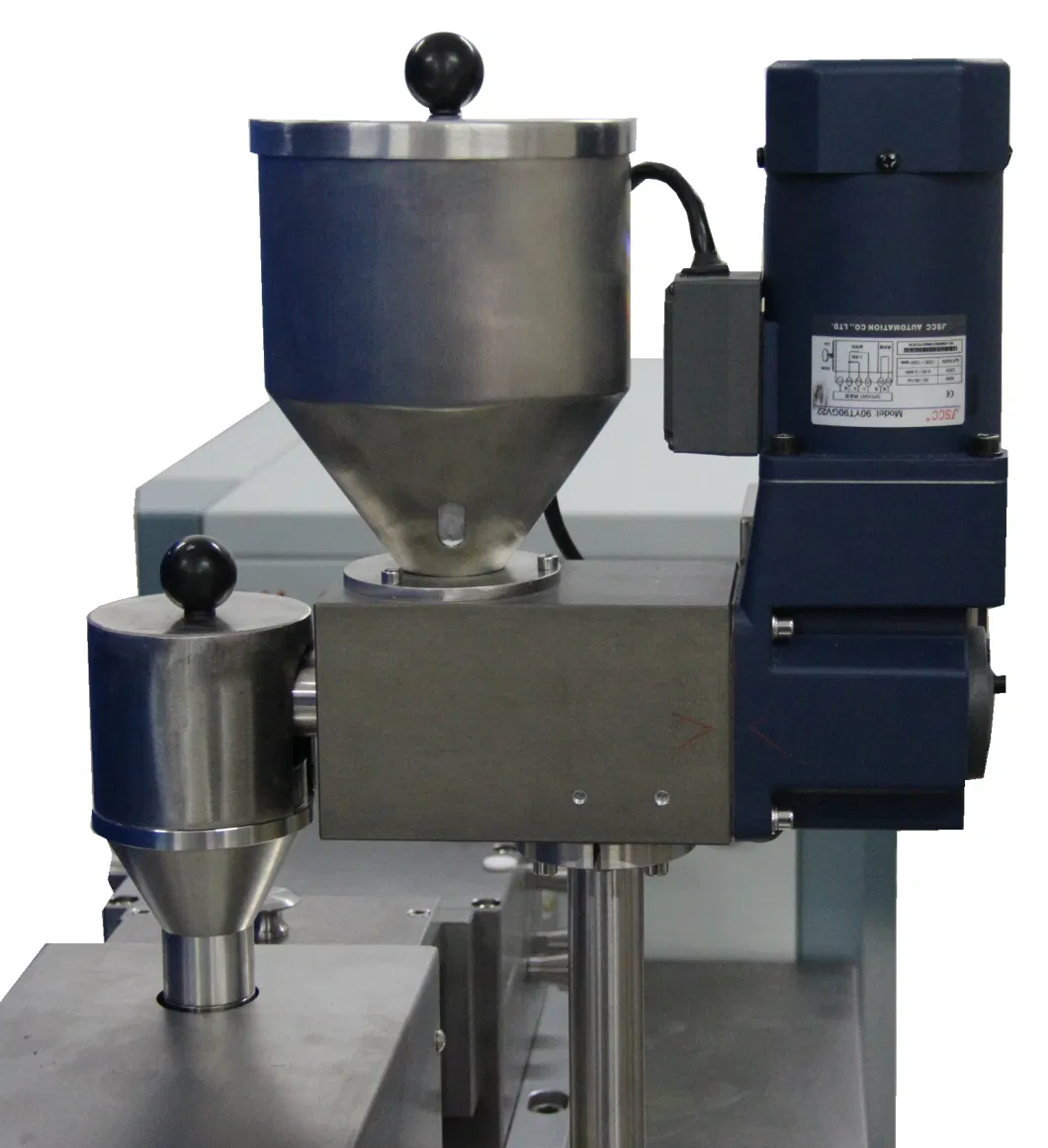
Barrel
Two threaded bores opposite each other are provided at the end of the barrel of each measuring extruder for taking a thermocouple and a pressure transducer for measuring the temperature and the pressure of the melt in front of the die channel. 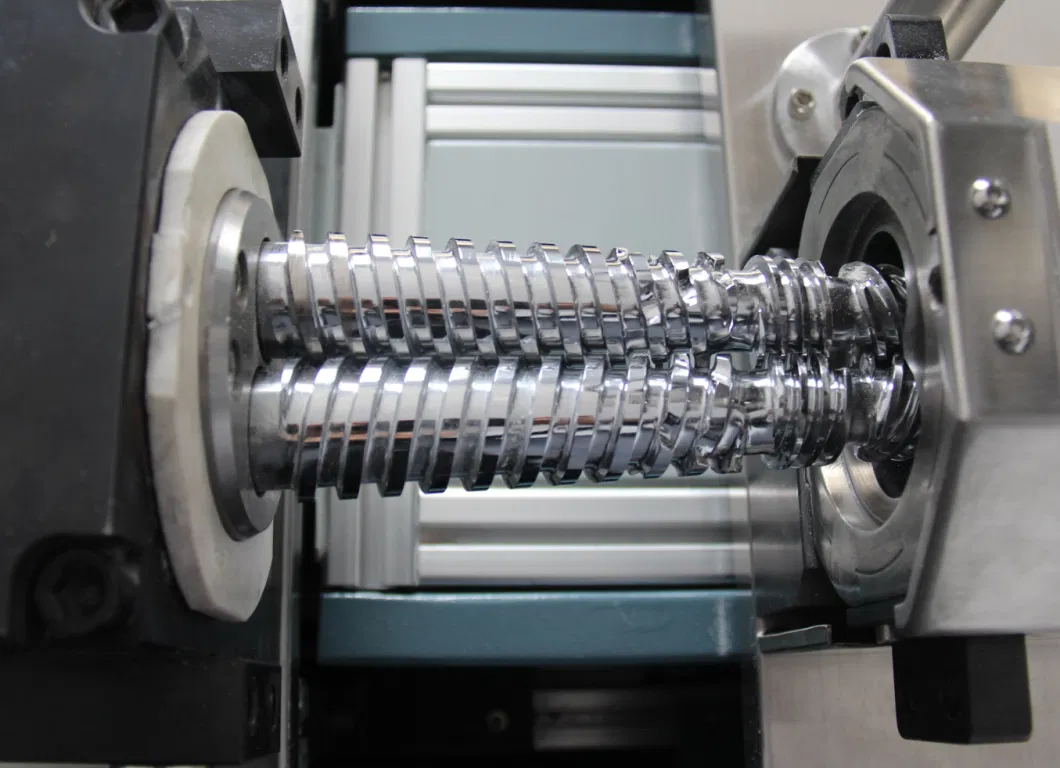
Screw
Because of its rotation, the powder or particle shape plastic was pushed to the former, so as to achieve compaction, melting and mixing purpose of homogenization. 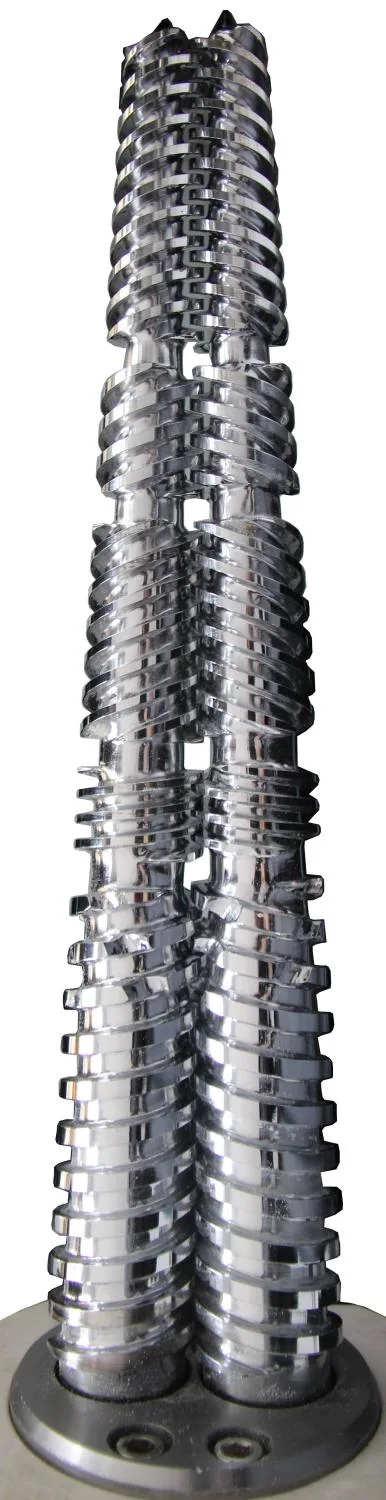
Dies
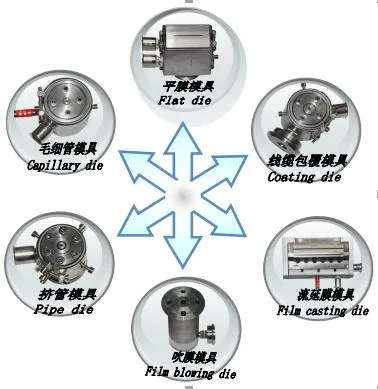
- Technical Parameters:
Photograph | Performance Index | Performance Parameter |
Barrel structure | Pull and turn | |
Screw Diameter | 20 mm | |
Screw Length | 325mm | |
Temp control system | RKC from Japan | |
Temp sensor | J type thermocouple | |
Heating | Electrical Heating/4 Zones | |
Heating power | 3.2 kW | |
Max. Temperature | 350ºC | |
Cooling | Air Compression | |
Pressure range | 0~100 Mpa | |
Feeding speed | Manual adjustment | |
Feeding | Screw metering feed | |
Output | 0.45 -11 kg/ hr | |
Die heads (Select one from three) | Flat Die ( L×W:60×1.5 mm, 0.8 kW) | |
Pipe Die (Inner Ф10, Outer Ф12.5, 0.6 kW ) | ||
Granulating Die( Ф3×2) | ||
Weight | 250 kg | |
Dimension (L×W×H) | 1000×570×1500 mm |
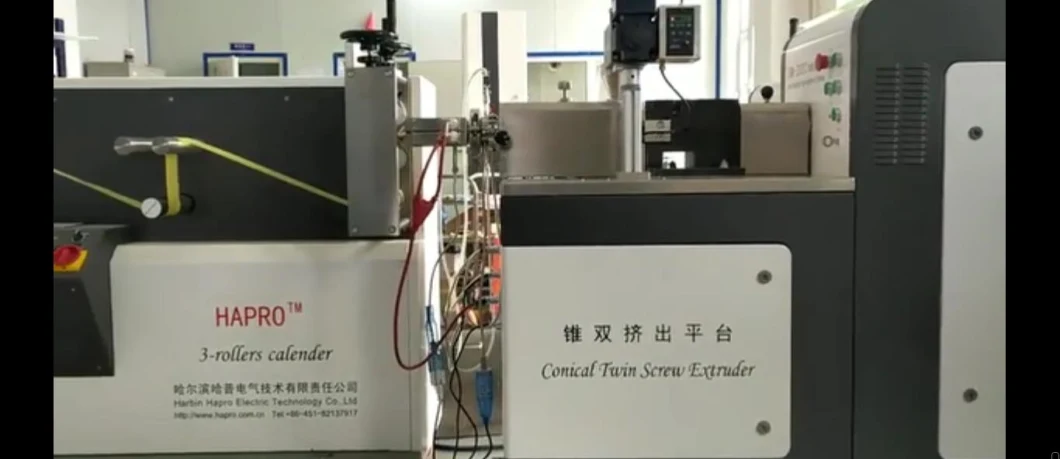
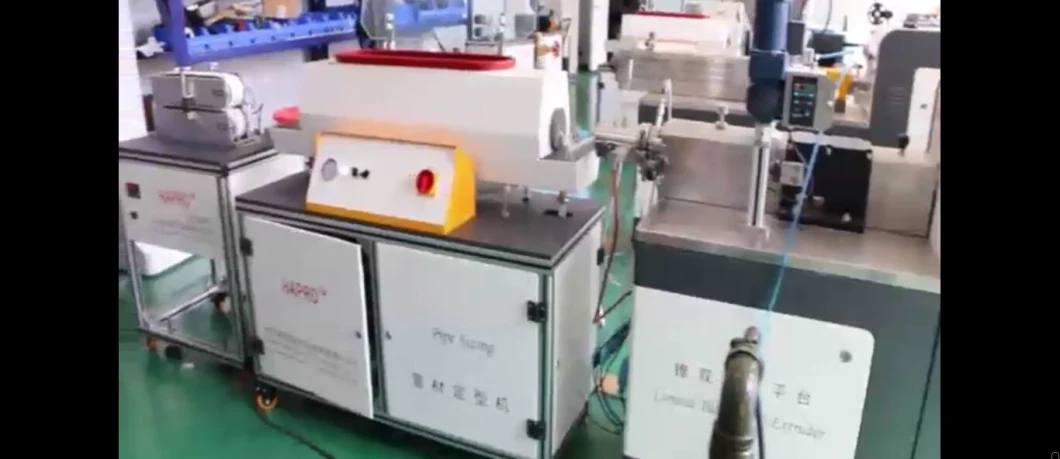