Basic Info.
Product Description

Sand Blast Room are mainly composed of blast room enclosure, guide rail and trolley, blasting media recovery system, ventilation dust collecting system, compressed air supply system, blasting system, lighting system and electric control system.
Bestech's air blast room eliminates many of the environmental problems and costs associated with chemical stripping you don't have to manage or dispose of hazardous liquids.
An Bestech sand blast room provides even greater potential for improving safety and reducing operating costs when you're cleaning, finishing or surface-profiling large work pieces. With the process contained in a specially designed enclosure, blast media and debris are isolated from external environment. And the operator, equipped with Bestech safety gear, is fully protected.
Abrasive transportation is another distinct advantage in the machine design. As well as the proven Scraper conveyor floor with its small installation depth, Bestech has extensive experience in screw conveyors and vibratory rows for abrasive transportation.
There is a choice between installation without foundation and low construction height or installation in an extremely flat foundation with low foundation costs.
Sand Blast Room is used for big components or components where automatic blasting would be too expensive. In combination with nozzle manipulators installed in the blastroom, surfaces can be automatically processed and areas that are hard to access can be blasted manually. Thus, the flexibility is maintained whilst reducing the number of blasters needed.
Key Benefits and Features of Blast Rooms
Bestech's blast rooms equip with automatic abrasive recovery system, and all kinds of economic types like floor trough type, sweep/shovel chute type, H type and U type are available.
Recovery system includes Abrasive Air Wash Mode.
The dust collecting system adopt pulse-jet cartridge type dust collector.
The cargo door and human door are equipped with door interlock.
Bestech's blast rooms adopt long lifespan LED light with integrated chip.
Bestech's sand blast room systems also include blast hose and variety of sized venturi blast nozzle
Bestech's blast tank are hydrostatically tested to operate at a pressure of 8 Bar (each blasting tank have their own certificates in accordance with GB 150.1-150.4-2011 and the only product coding).
Applications of Blast Rooms
Surface Preparation: Beams, metal sheets, pipes/tubes, slabs, big welding constructions
Smoothing: Pickled or eroded surfaces, machining lines, etc.
Decorative Blasting: Light metals, stainless steel, copper, brass, etc.
Peening: Parts exposed to high stress, torsion bars, etc.
De-burring: Flame cut, sawed and stamped parts
Sand Blast Rooms
Blast Rooms are mainly composed of blast room enclosure, guide rail and trolley, blasting media recovery system, ventilation dust collecting system, compressed air supply system, blasting system, lighting system and electric control system.
Bestech's blast rooms eliminates many of the environmental problems and costs associated with chemical stripping you don't have to manage or dispose of hazardous liquids.
An Bestech blast room provides even greater potential for improving safety and reducing operating costs when you're cleaning, finishing or surface-profiling large work pieces. With the process contained in a specially designed enclosure, blast media and debris are isolated from external environment. And the operator, equipped with Bestech safety gear, is fully protected.
With an Bestech blast room, you can select from a range of proven components for media recovery and reclamation. In addition, we offer many accessories and options designed to maximize productivity in the context of different working environments.
In other words, a room consisting of standard Bestech components will meet most application requirements economically.
Scraper Media Recovery Floor
On the reverse stroke the rubber scraper blade, unhindered in this direction by the steel comb, is free to pass over the previous scrappers deposit of abrasive (B). The abrasive is pushed forward to a final corridor positioned at right angles to the booth where it conveys the abrasive to an elevator and is recycled.
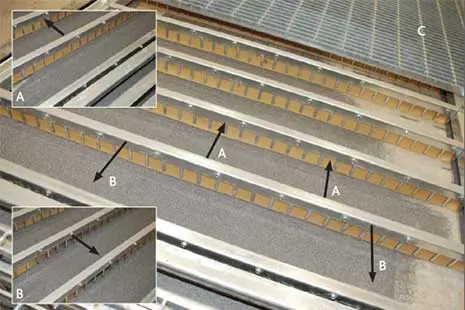
The depth of the recovery channel is only 130mm ensuring that in many instances, ie. Those where objects being taken into the booth may be carried by hand, it can be located directly onto an existing factory floor. When a flush finish is required between the factory floor and the blast room, only minor excavation is required. The scraper system is covered by a pedestrian grating (C) on which the operator stands and through which the abrasive falls. In certain applications when heavy items are being processed, this grating can be increased in strength to provide greater loading capacities. An alternative method of supporting a heavier item is to incorporate rails into the floor, positioned conveniently between the recovery corridors on which a bogie can be mounted.

size of workpiece (m) | 3*2.6*2.0 | 4.5*3.5*2.5 | 7.5*5*3.8 | 26*3.1*4.6 |
carrying capacity (t) | 3 | 5 | 20 | 80 |
power(kw) | 37 | 40 | 86 | 186 |

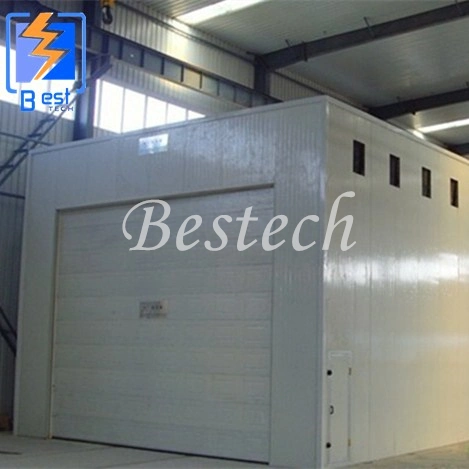


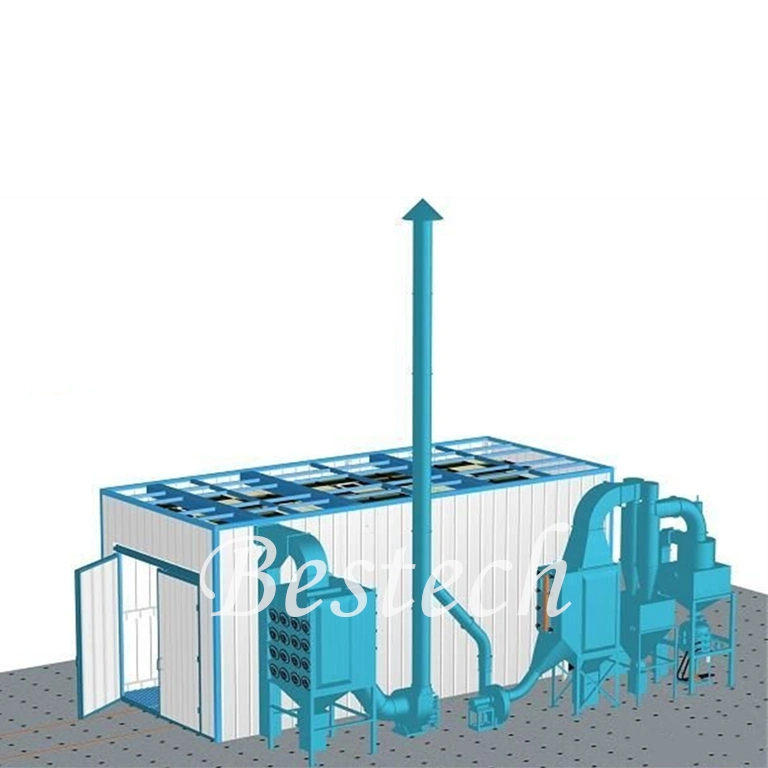

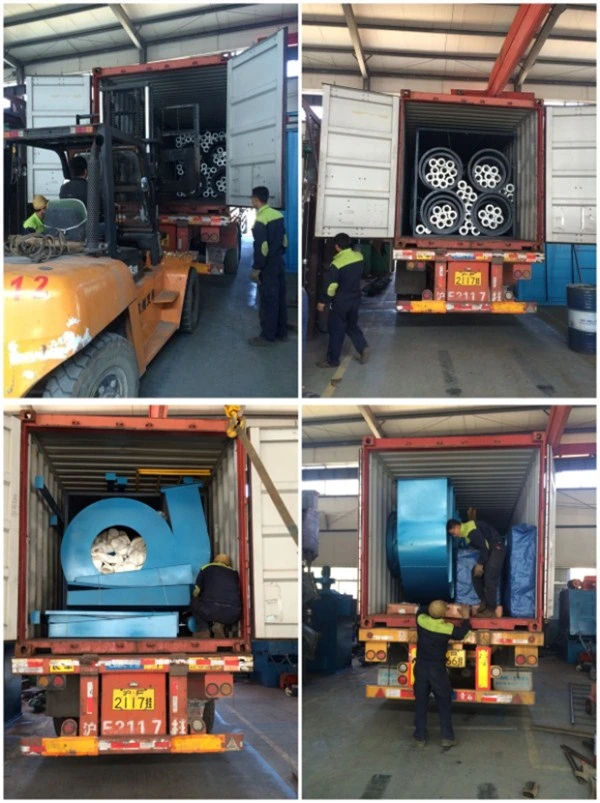
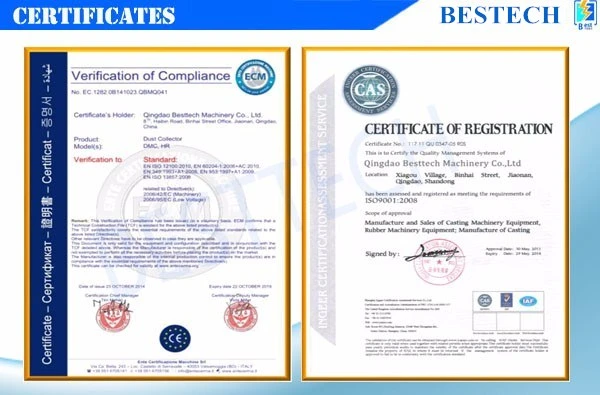
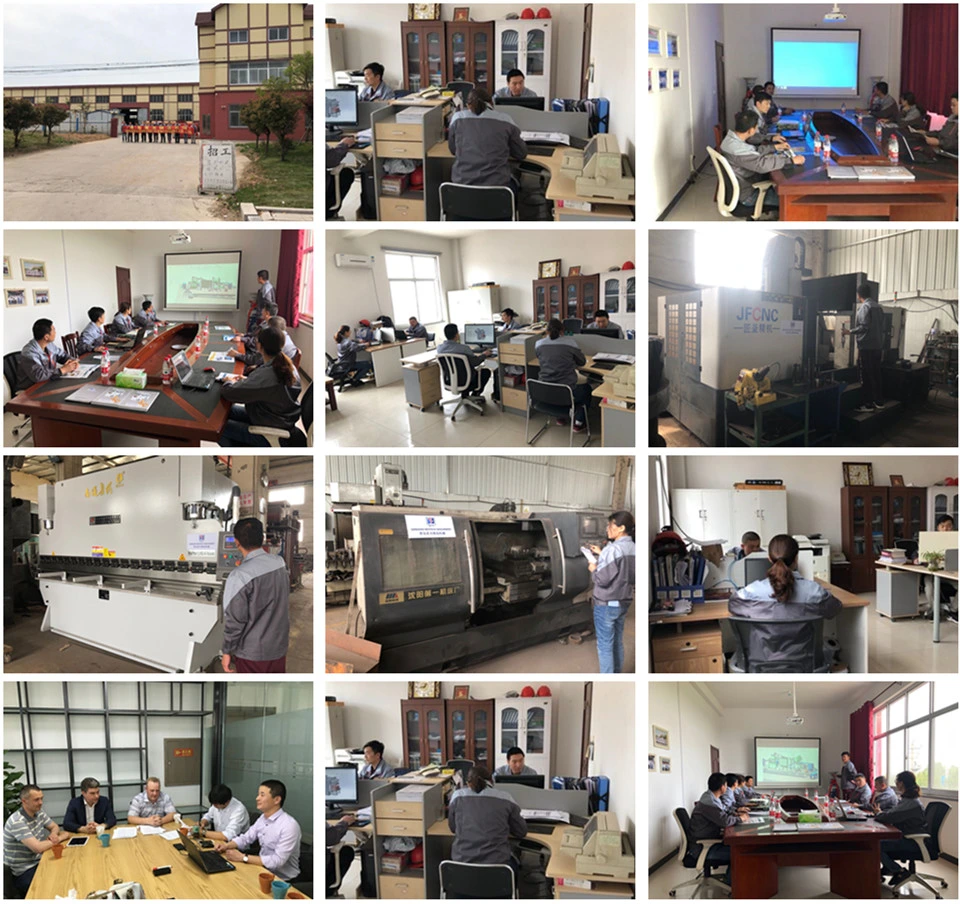
Our service
1. Reply your inquiry in 24 working hours.
2. Experienced staffs answer all your questions in fluent English.
3. Customized design is available. UEM&UBM are welcomed.
4. Exclusive and unique solution can be provided to our customer by our well-trained and professional engineers and staff.
5. Special discount and protection of sales are provided to our distributor.
6. Professional factory : We are manufacturer, specializing in producing all kinds of machinery for more than 20 years, competitive with good quantity.
7.Sample: We can send out sample for test in one week if the order quantity is big enough. But the shipment charges is usually paid by your side, the charges will be rebounded when we have formal order.
8.As an honest seller, we always use superior raw material, advanced machines, skilled technicians to ensure our products to be finished in high quality and stable feature. Welcome to contact us or visit our company.